Led by Lithium pioneer Iggy Tan and the ‘Dream Team’, Lithium Universe (ASX: LU7) has a bold vision of closing the Lithium Conversion Gap in North America by building a vertical integrated mine-to-battery-grade lithium conversion facilities in Canada and help the world transition towards cleaner energy.
Lithium Carbonate Refinery
Overview
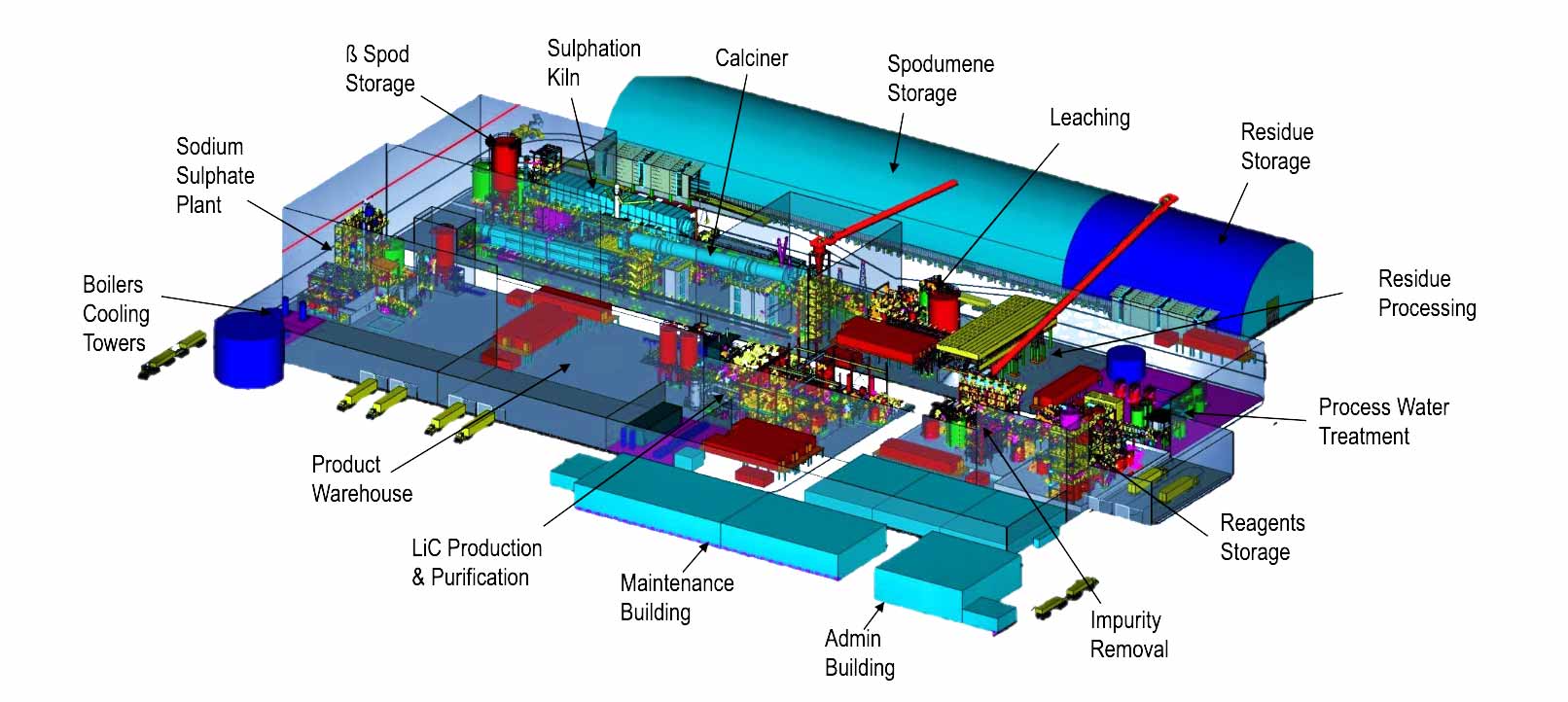
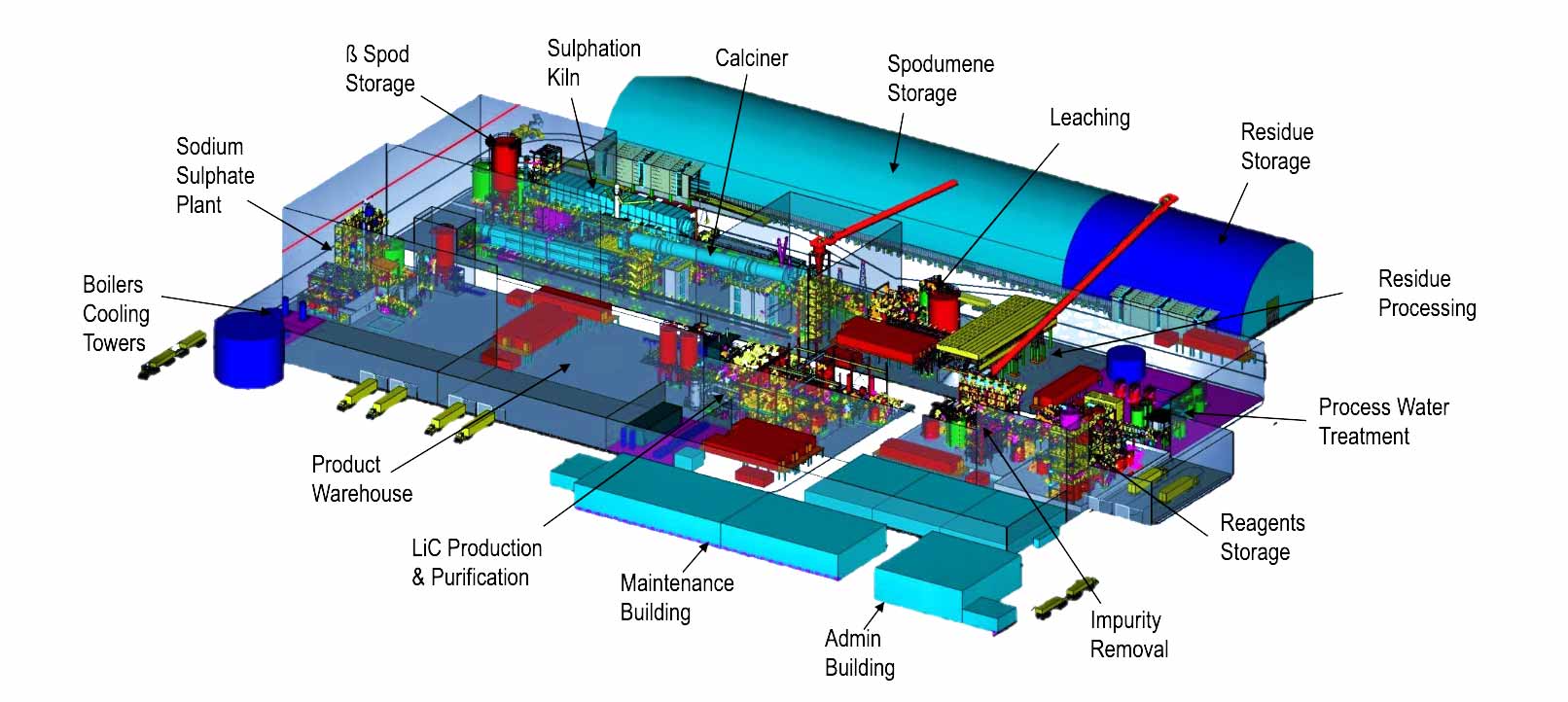
Figure 1: Bécancour Lithium Refinery 3D Model
Building on this success, Lithium Universe plans to replicate the Jiangsu plant’s design, utilizing the same suppliers, equipment, and engineering firm to mitigate technical risks plaguing other Western lithium refinery operations.
Hatch Limited, the engineering company behind the original Jiangsu plant, has been contracted to conduct the Engineering Study to support the Company’s Definitive Feasibility Study (DFS) for the Bécancour Lithium Refinery.
Hatch is a renowned global engineering company, boasting a vast network of over 15,000 professionals and operating in more than 150 countries worldwide. With its origins in Canada, Hatch has extensive experience in successfully delivering lithium-based projects in Québec and globally. Hatch has more than 70 years of project delivery experience in Québec and has pioneered the use of modular construction in the region. Furthermore, Hatch who worked closely with Lithium Universe Chairman Iggy Tan and Dr Jingyuan Liu, on the design and delivery of the 17,000 tpa Jiangsu Lithium Carbonate Plant, operated by Galaxy Resources Limited.
The design will include the use of conventional kiln conversion of spodumene, sulphuric acid sulphation and leaching, impurity removal and final purification to battery-grade quality lithium carbonate, similar to that of the Jiangsu Lithium Carbonate Plant.
Site location selection for the lithium refinery is now complete and Lithium Universe has secured prime industrial property in the Bécancour Waterfront Industrial Park. This location is close to hydroelectricity, gas, road, rail infrastructure and spodumene import facilities.
The Company has officially submitted an application for up to 22.5 MW of green electricity (Train 1) to Hydro-Québec. The Company estimates that using hydroelectric power from Quebec could reduce greenhouse gas emissions by up to 95% compared to other refineries that rely on coal-fired power plants.
Important Updates
Spodumene Concentrator
Lithium Universe Limited has appointed Primero Group Limited (Primero) as lead manager in relation to the design of a multi-purpose stand-alone concentrator to be based in Canada.
WATCH: Lithium Universe Chairman Iggy Tan discusses the appointment of Primero Group Limited as the lead manager to the design of a multi-purpose stand-alone concentrator in Canada.
This appointment the Primero Group to undertake the design of a Lithium Concentrator is part of Lithium Universe’s Québec Lithium Processing Hub (QLPH) strategy.
Founded in 2011, Primero specialises in providing design, construction, and operational services for resource projects worldwide. With extensive experience in the lithium sector, Primero’s vertically integrated business model provides for Build, Own, and Operate (BOO) capabilities, enabling its clients to conserve their capital expenditures whilst expediting the transition from an exploration-based, to production-based business operation.
The appointment of Primero to undertake the Concentrator Engineering Study follows an extensive process to procure a contractor with the suitable experience and capabilities to undertake the design of a stand-alone concentrator with the ability to process 1 Mtpa of spodumene ore. The expected design is anticipated to be similar to that of the Mt Cattlin plant, which uses a simple dense media separation (DMS).
The finalized design flow sheet outlines a four-stage crushing process to generate crushed ore ranging from 0.85mm to 6mm in size. Any crusher fines smaller than 0.85mm identified by the screens will undergo processing in a dedicated flotation unit. The spodumene recovered from this process will undergo drying and then be blended with the final spodumene concentrate. Additionally, any mica present in the crushed ore will undergo removal using a reflux classifier. Subsequently, the material will be split into two streams: one less than 3mm and the other greater than 3mm. Both streams will be directed through two-stage dense media separation units. The less than 3mm stream will undergo mica removal via a reflux classifier at the initial stage. The recovered spodumene from both streams will be combined through blending and stored in a dedicated storage shed. To ensure functionality in the Québec climate, the entire plant will be winterized. See Figure 1 for final flow sheet.